"Courtesy Sandia National Laboratories, SUMMiT™ Technologies, www.sandia.gov/mstc"
We require credit be placed prominently near or underneath the photo or movie.
Thank you for using our web site.
MEMS Videos
World’s Smallest Mite-Go-Round
Two dust mites taking a spin atop an optical shutter running at low speed. The mites’ limbs are flailing due to the slickness of the silicon wafer.
Aphid on Micromirror
This aphid (considerably larger than the dust mites) crosses a micromirror, catching his feet on suspension springs as he travels. Note the mirror still operates after being bug-stomped.
Spider Mite Crossing Large Gear
This spider mite is on construction duty; as he crosses the large wheel, he leaves a gear guide for future assembly. Silly bug – doesn’t he know that these systems are batch fabricated and no assembly is required?!
Spider Mite Riding Large Wheel
This spider mite decides to ride the large wheel as it reverses directions.
Spider Mite Test
This micromirror continues to be operational even after being tested by the spider mite.
High Speed, Low Drag
This clip shows that Sandia MEMS motors can rotate large wheels and drive a substantial load (the spider mite), all at very high speeds. Future wheels may include spider mite handrails.
Comb Drive Close-up
This is a close-up view of a microengine comb drive in operation. The visual contrast changes with the electrostatic charge.
Comb Drive Wide Field
This video presents a wider view of the visual contrast changes.
Signal Lines
The lines delivering the drive signal to the comb drives of our running microengine are visible in this video. As above, the visual contrast changes with the applied voltage.
Bond Pad
In the lower left corner of these frames, is the wire which transmits the drive signal from the power source. The wire is attached to the bond pad of the microengine, from which the signal flows along traces to the microengine.
Gear Powered by Microengine
This is a gear being driven by one of our microengines. The SEM provides unprecedented magnification, although when viewing moving objects, real-time, the detail visible is a fraction of that of a still image.
Gear Hub Close-up
This is a close-up look at the hub of a moving gear. The greatest advantage of running MEMS in an SEM is the ability to view wear on moving parts, real-time, at extreme magnifications.
Linkage Arm and Comb Drive
The linkage arm and comb drive, using our voltage visual contrast technique to show where the voltage is as it drives the engine.
Comb Drive Wide View
Here is a wider view of the microengine in operation, which more clearly shows how the voltage changes on the combs pull and release the engine so that it moves back and forth like a piston.
Six-gear Planar Train
There is a trick to keeping the gears in this six-gear train correctly meshed when they are only about two microns thick – they are held in plane by flat guide plates which are mounted to the tops of the shafts.
An Overview of the Six-gear Planar Train
Six-gear planar train operating at variable working speeds.
Six-gear planar train operating at a fast speed.
Close-up video of the six-gear planar train in operation
Five-gear Planar Train
In this clip is a chain of 5 gears of various sizes being driven by a microengine moving at the amazing speed of 60,000 RPM.
Transmission Driving "Large" Gears
Here a transmission drives two of our largest gears – each is more than a millimeter in diameter.
Transmission Driving "Large" Gears – Clip Two
The two large gears are being driven by a microengine operating at 6000 RPM. The transmission has been driven at speeds as high as 60,000 RPM.
Spring Device
Here a spring device is wound and unwound. Perhaps one day a micro-clock can be made with this type of mechanism.
Spring Device – Clip Two
In this video, the spring is wound and unwound by a microengine operating at 6000 RPM.
Linked Gears
Here, a transmission drives two linked gears while the microengine runs at 60,000 RPM.
Torque Demonstration
This is a microengine driving a gear approximately 40 times its own diameter, demonstrating the large torque it can produce.
Microengine and Gears
This microengine’s drive gear is turning a 250-tooth gear more than 10X as large as itself. The speed of the drive gear is 600 RPM, and it has been operated as fast as 60,000 RPM.
Microengine, Transmission, and Spring Device
This video pans from the microengine driving the device, through a transmission that multiplies the torque, to a spring that winds-up and drives additional gears.
Linear Rack
A comb drive actuator rotates a drive gear, which in turn drives a linear rack back and forth to its full extents.
Linear Rack (High Speed Operation)
The same linear rack as above, operating at full speed (less than 0.04 seconds travel time).
Pop-up Silicon Mirror
Force provided by a comb drive actuator moves a linear rack, which drives a hinged sheet of silicon back and forth. A HeNe optical-band (red) laser is focused at an angle such that as the mirror is elevated, the coherent light is reflected into the microscope’s camera.
Pop-up Silicon Mirror (High Speed Operation)
The same pop-up mirror as above, this time operating at full speed. The high switch rate of the mirror (35 milliseconds) validates its potential for use in optical switching.
Pop-up Silicon Mirror (High Speed Operation)
Although just a blur, this is actually the mirror being raised and lowered by a microengine operating at over 100,000 RPM.
Deflection of Laser Light
Here a mirror is slowly raised and lowered to show the deflection of laser light.
Pop-up Silicon Mirror
In this video, the mirror is shown being elevated in less than two-thousandths of a second.
Demonstration of Switching Speed
The switching speed (time required to deflect optical energy) can range from 2.67 milliseconds for fullly raising and lowering the mirror to 1.18 milliseconds for smaller angle deflections.
Torsional Ratcheting Actuator
The torsional ratcheting actuator (TRA) is running at a slow, constant speed. By visually following the dot on the outer ring which starts out at 3 o’clock position, the ring’s rotation can be seen.
Torsional Ratcheting Actuator Close-up
In this close-up, the camera pans across the lower half of the TRA device. Again, it is running slowly so its motion is clearly visible.
Torsional Ratcheting Actuator
As the camera finishes panning to the bottom right corner of the TRA, you can see our Sandia National Laboratories Thunderbird Logo. To put the size of the TRA in perspective, it is approximately one-third the size of our comb drive microengines.
Torsional Ratcheting Actuator
In this video and the next, the TRA is put through its paces; the TRA’s speed is doubled at regular intervals – from a 1 Hz drive signal up to 640 Hz – then it is slowed down again.
Torsional Ratcheting Actuator
Please note that the dot on the outer ring is moving almost too fast to see! We have operated the TRA with drive signals in the low kHz range, and will be able to increase that still further with future refinements.
Torsional Ratcheting Actuator Pawl Close-up
In this close-up of the ratcheting pawl (with black dot) operating at low speed, it is possible to see that with each cycle it pulls one tooth on the outer ring.
Rotary Motor
The rotary motor is operating at various speeds in this video.
Rotary Motor
In this video, the camera pans to the center of the rotary motor and then out to its edge.
A Newer Version of our Rotary Motor
The rotary motor operating at high speed.
A Newer Version of our Rotary Motor
The rotary motor operating at medium speed.
A Newer Version of our Rotary Motor
The rotary motor operating at slow speed.
Wedge Indexing Motor (Slow)
Wedge Indexing Motor (Medium)
High Speed Optical Shutter
The optical shutter directs a beam of light by passing it through apertures in the shutter. Here we demonstrate (real-time footage!) a switching time of 35 milliseconds.
2-Bit Binary Encoder
The binary encoder wheel stops in any of four positions, each of which is associated with a particular shutter aperture. A single beam of light would be capable of up to four signals based on the wheel’s orientation.
World’s Smallest Microsteam Engine
Water inside of the compression cylinder is heated by a flow of electric current and vaporizes, pushing the piston out. Capillary forces then retract the piston when the current is not flowing.
Opal
The video shows micromirrors that are erected on a rotating stage. A torsional ratchting actuator (TRA) and a gear transmission are used to turn the stage. The angled mirrors reflect a green LED that is positioned to reflect light into a video camera.
Short Stage
In this video clip a 16 mg solder ball that hangs over the edge of the stage had been placed on top. The actuators are still able to rotate the stage with the large (for MEMS) additional load and friction.
Plate Gyro
This video shows a capacitively coupled MEMS rotating stage with an on-board accelerometer. A thermally actuated ratchet rotates the stage in precise increments utilizing a 7 V square wave signal.
Plate Gyro with Si
A small silicon part has been placed on top of the rotating stage in this expanded view video. The two thermal actuators can be seen ratcheting the stage through a few degrees of rotation.
Plate Gyro with Solder Ball
In this video a 2 mg solder ball has been placed on the stage. The actuators have no problem rotating the stage with the added weight and resulting friction.
MEMS Images
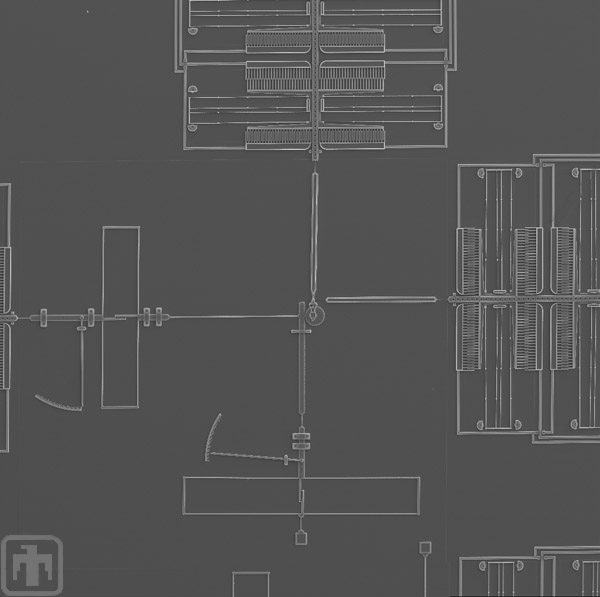
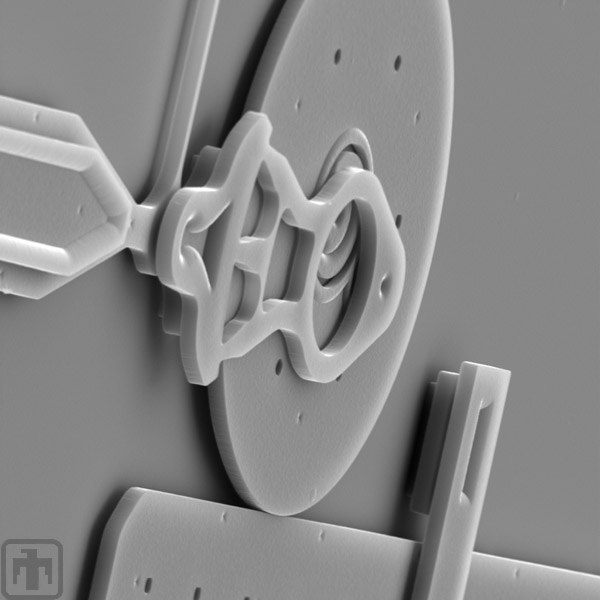
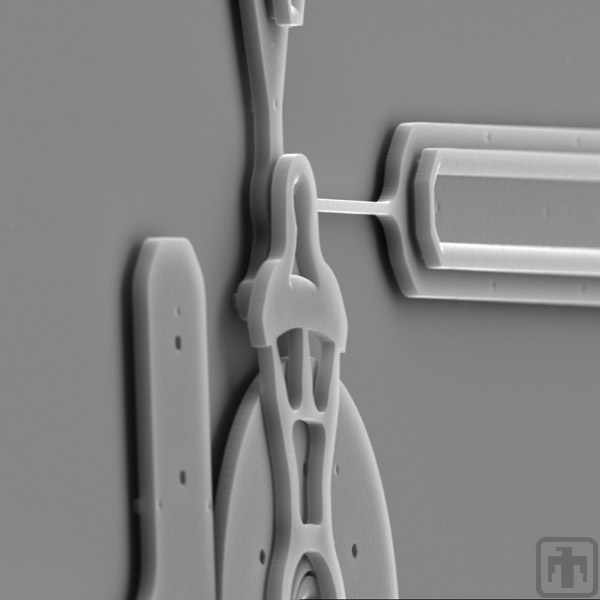
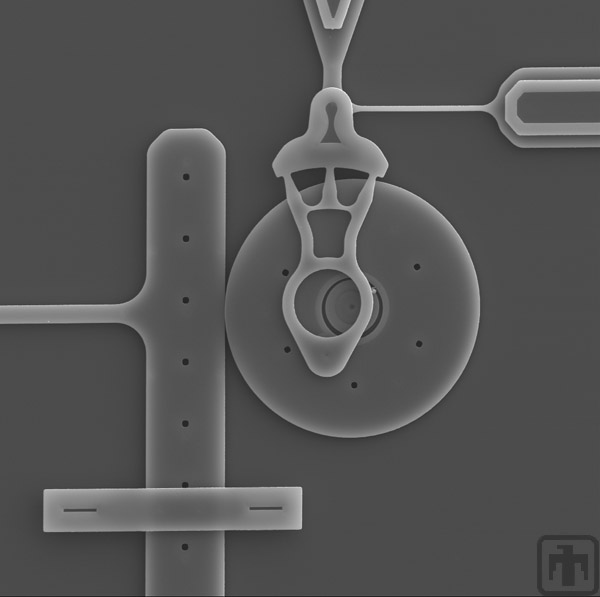
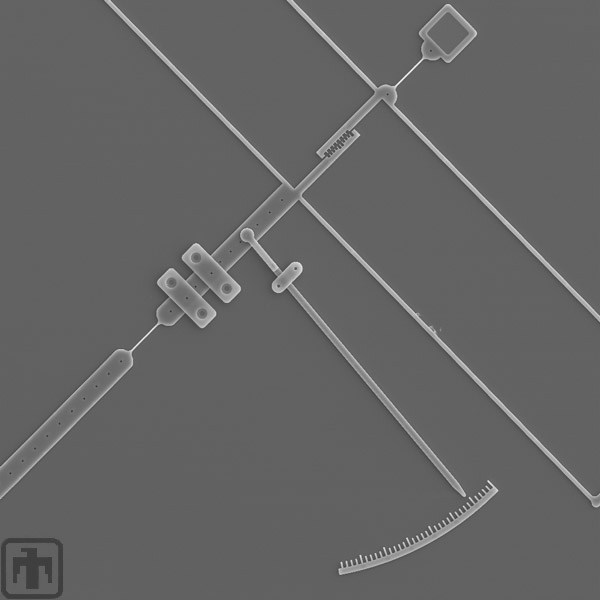
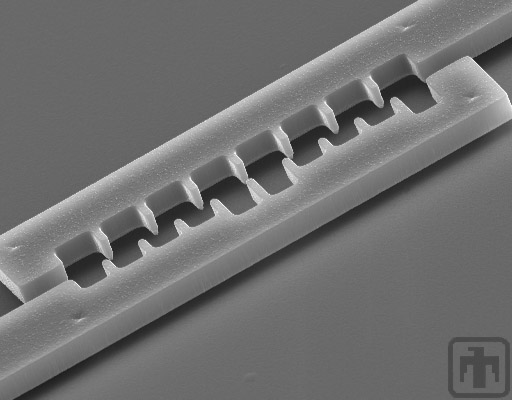
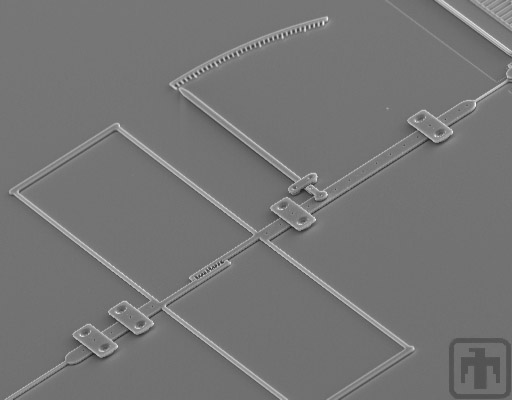
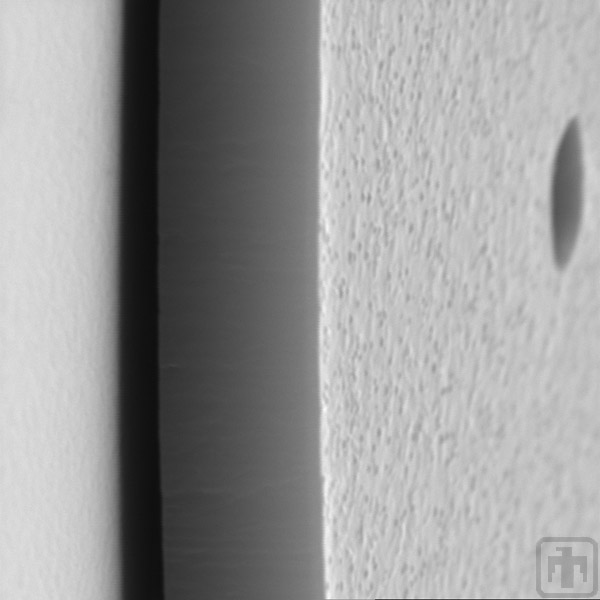
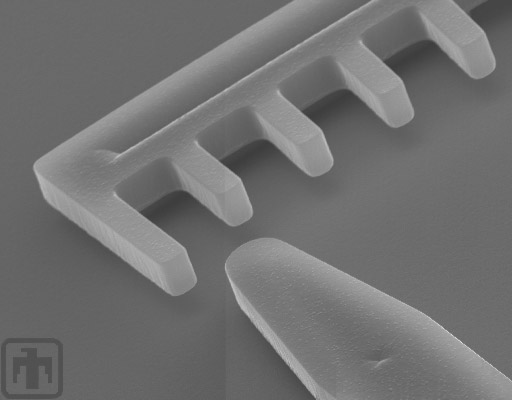
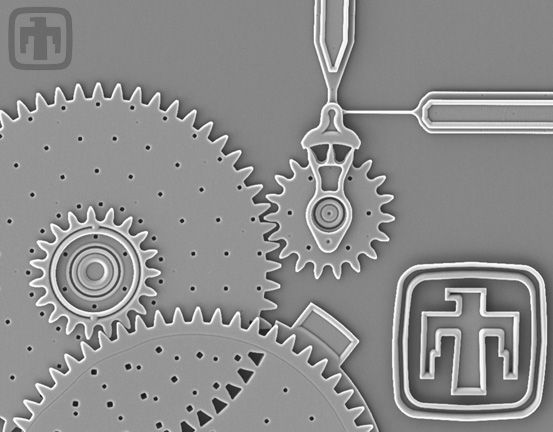
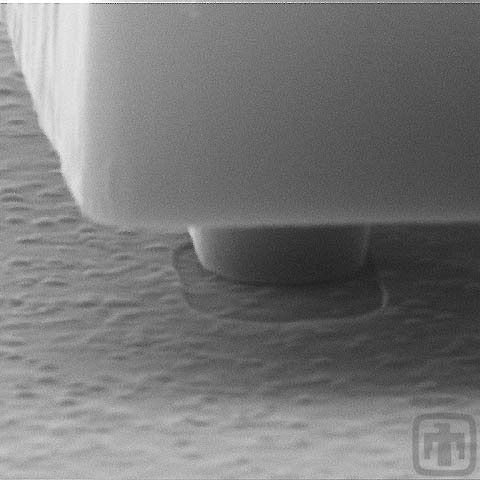
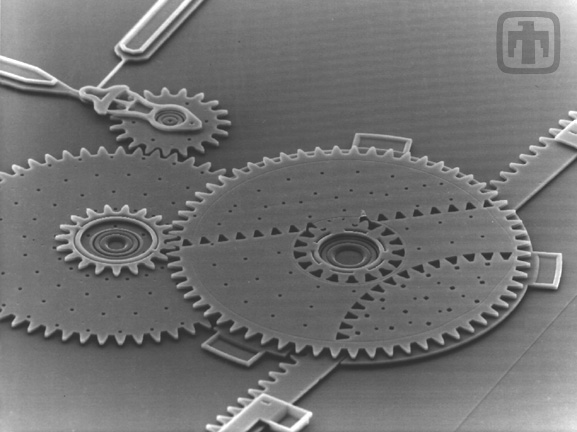
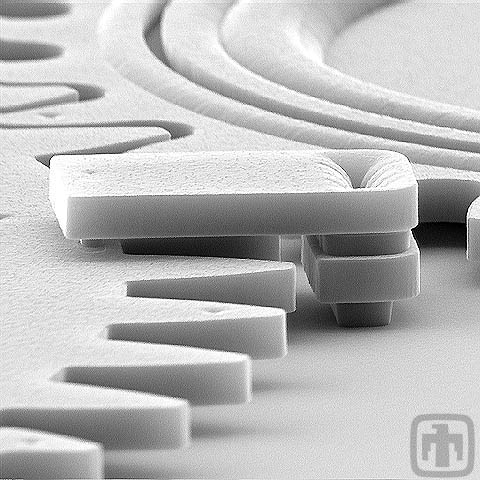
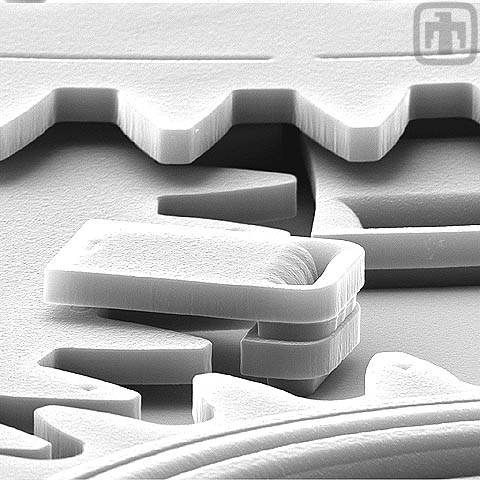
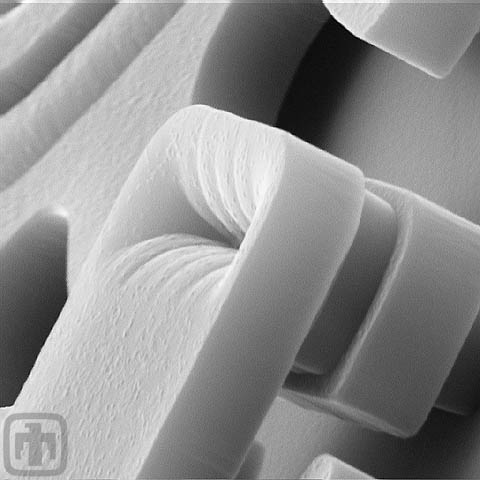
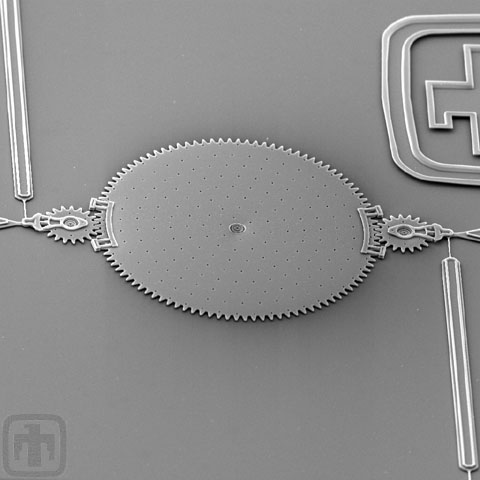
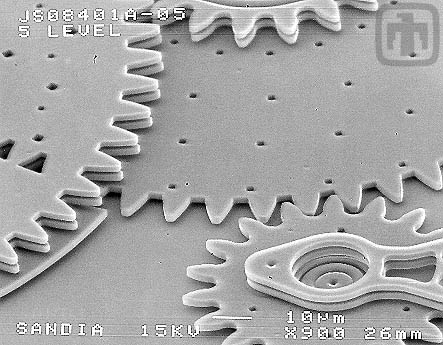
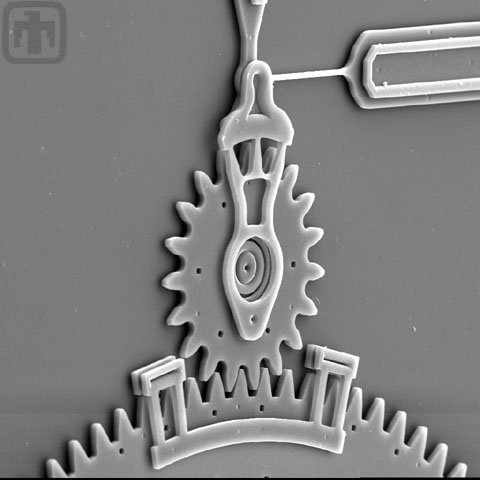
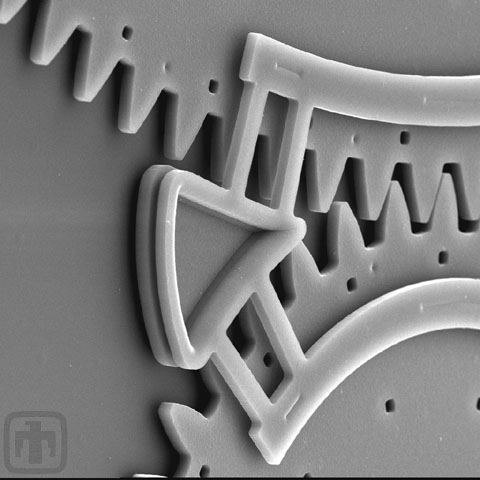
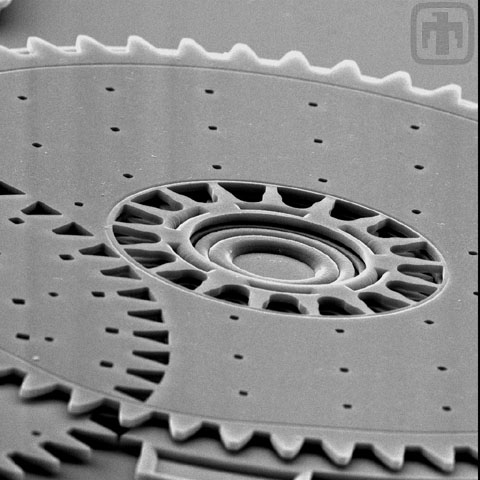
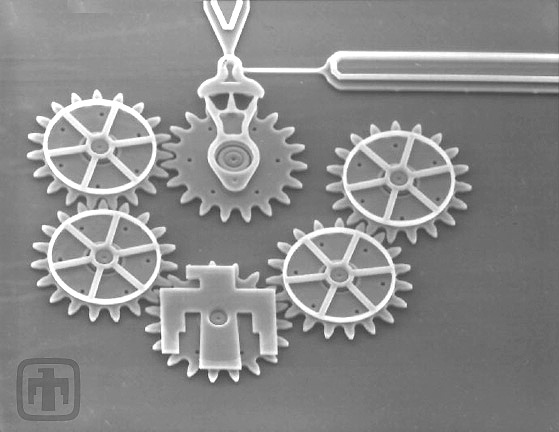
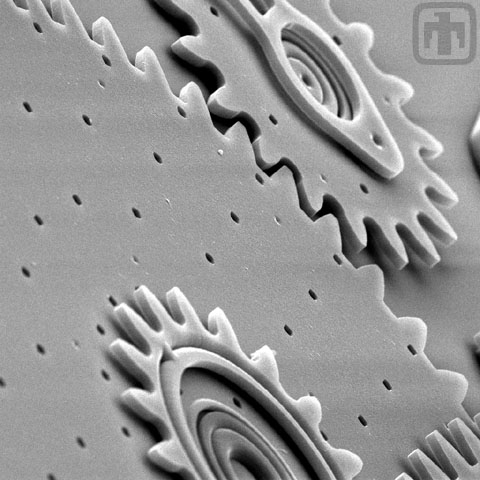
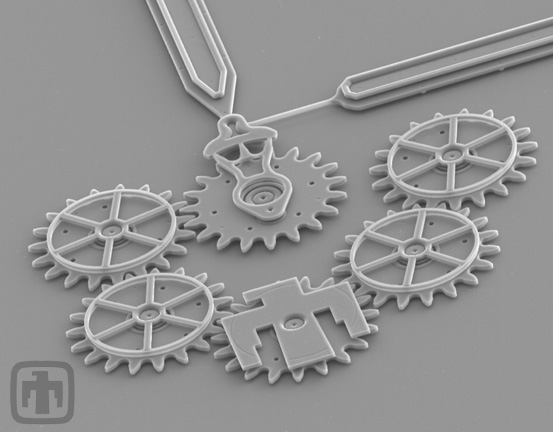
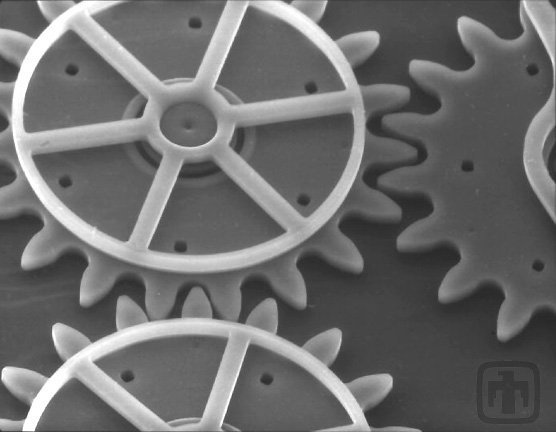
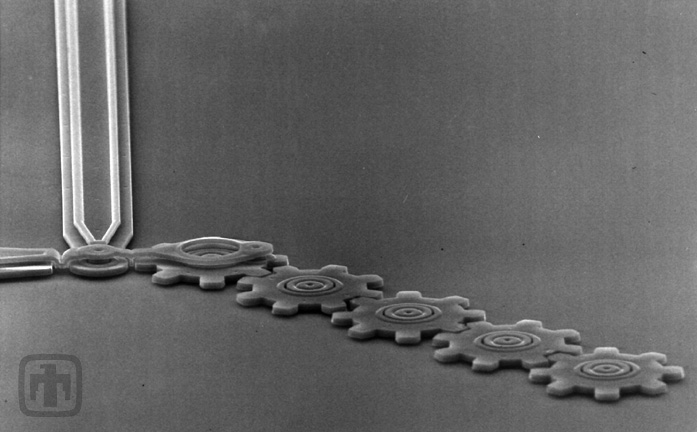
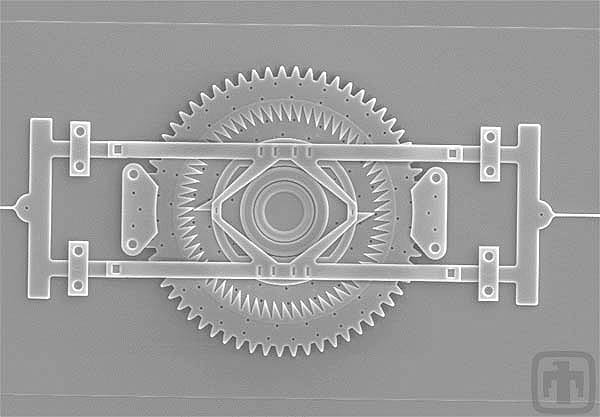
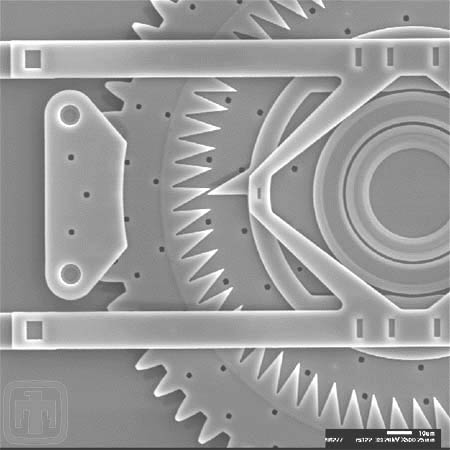
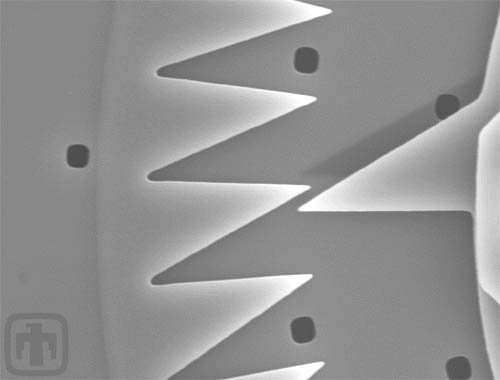
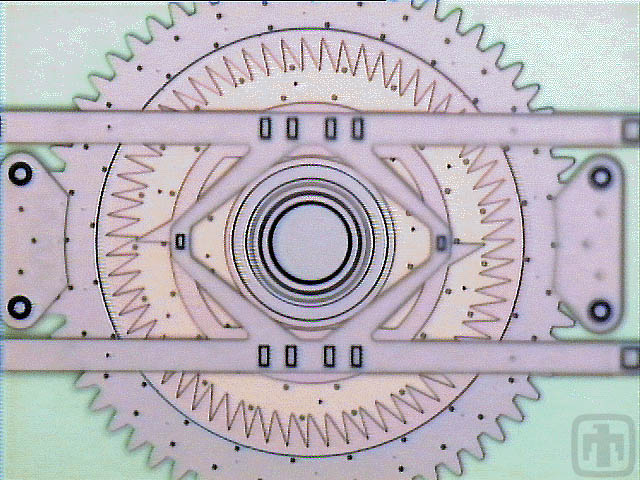
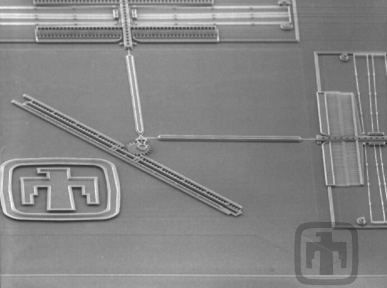
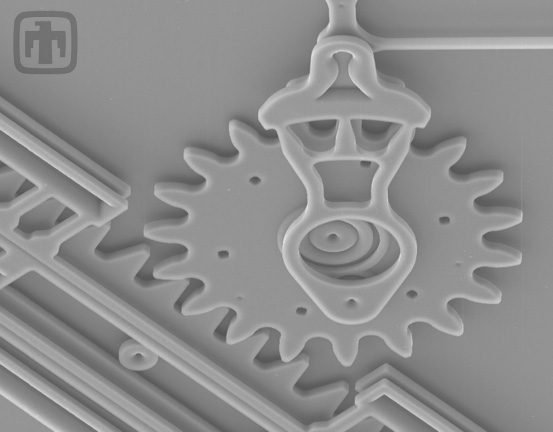
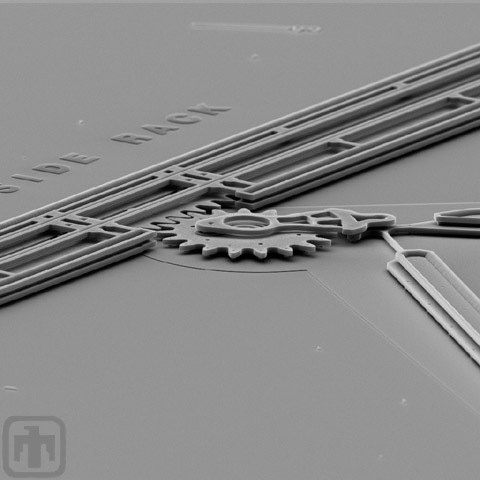
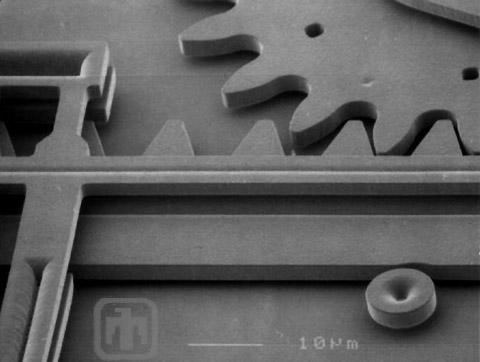
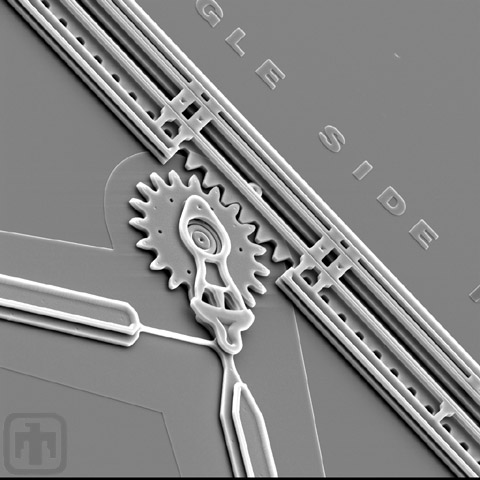
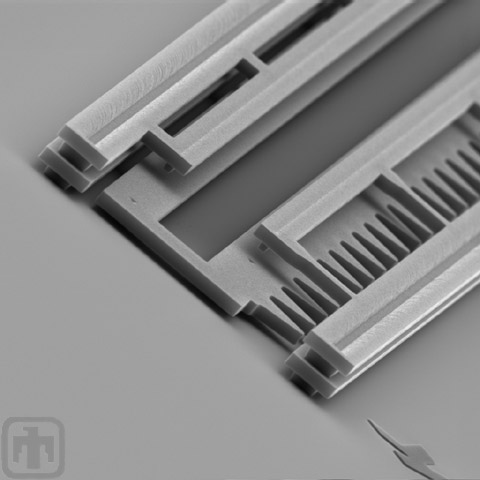
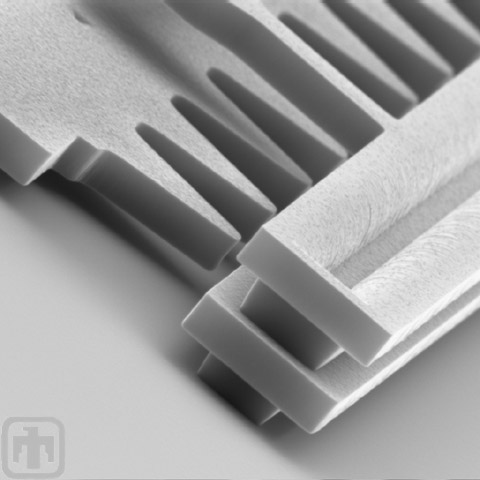
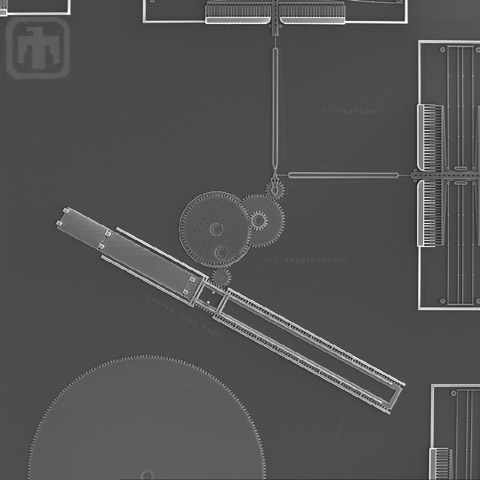
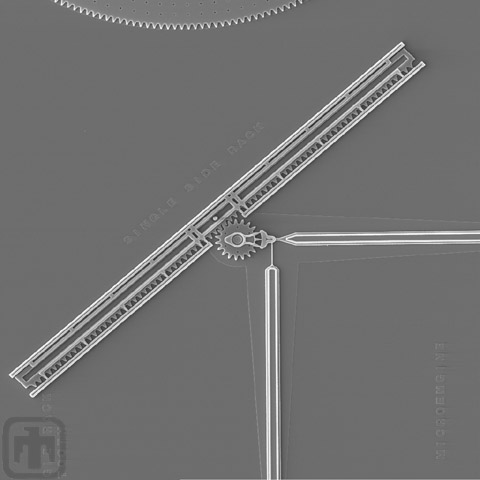
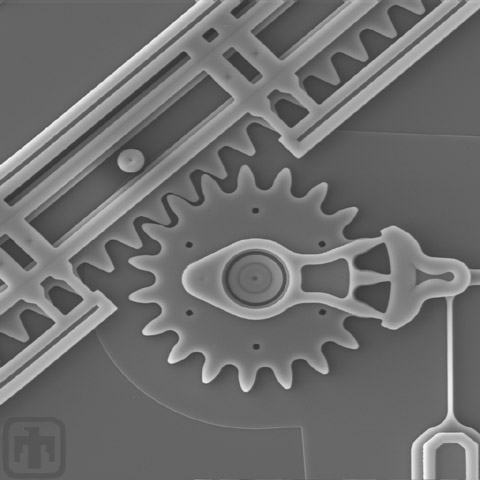
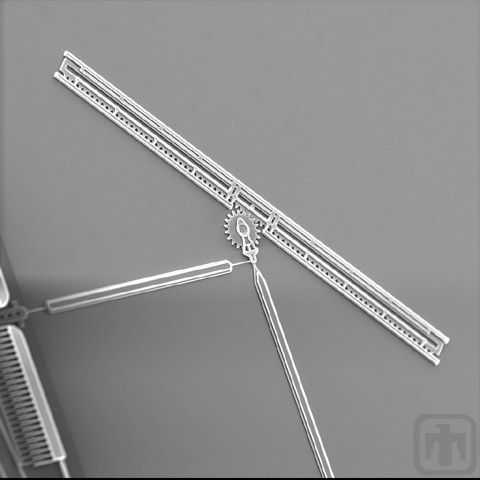
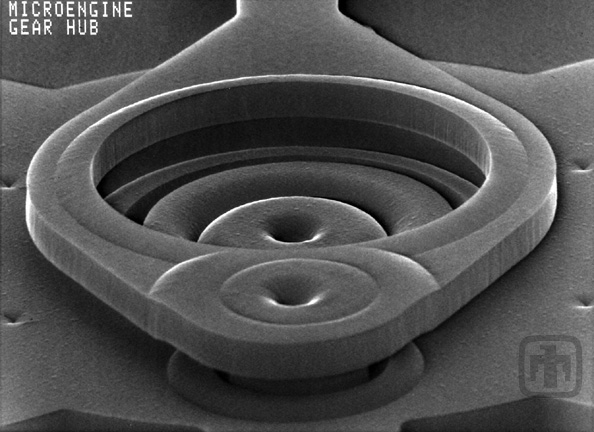
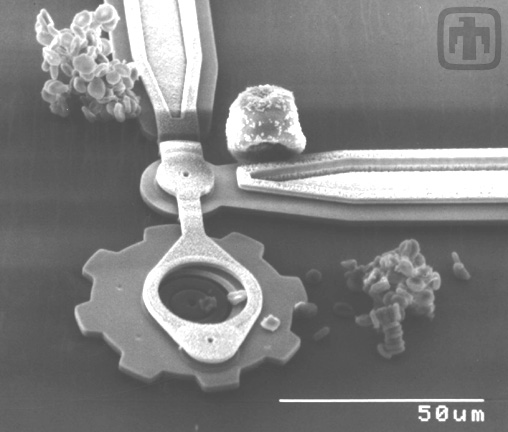
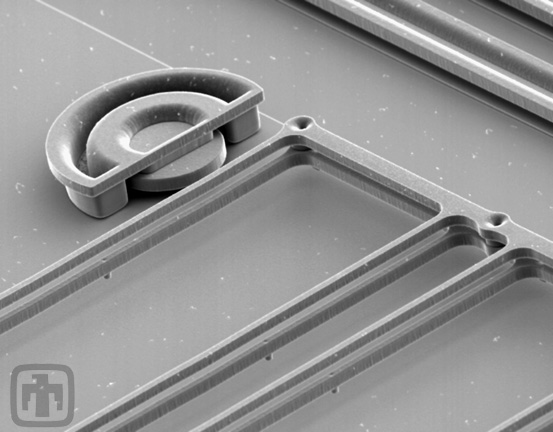
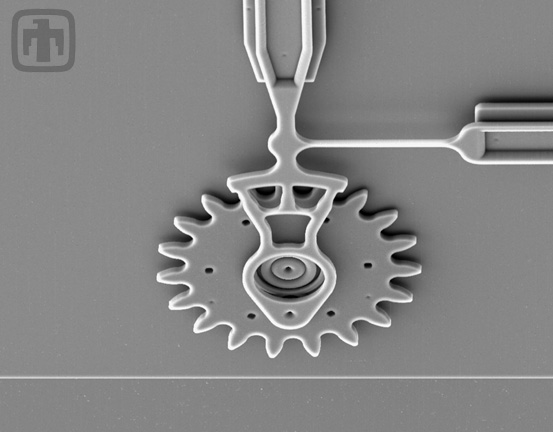
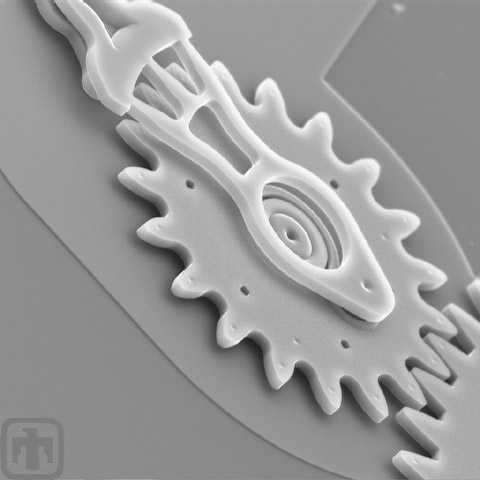
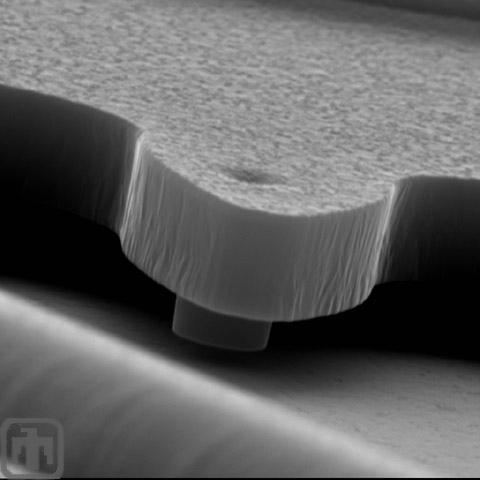
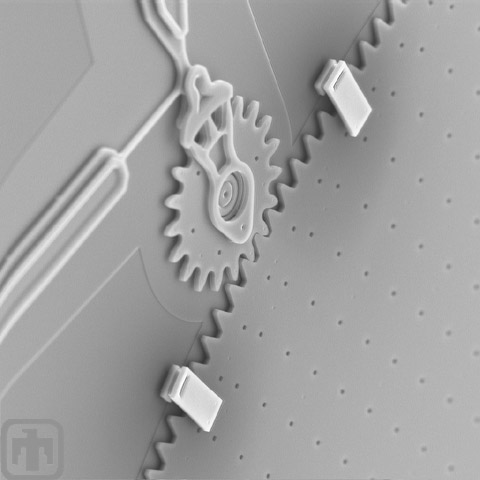
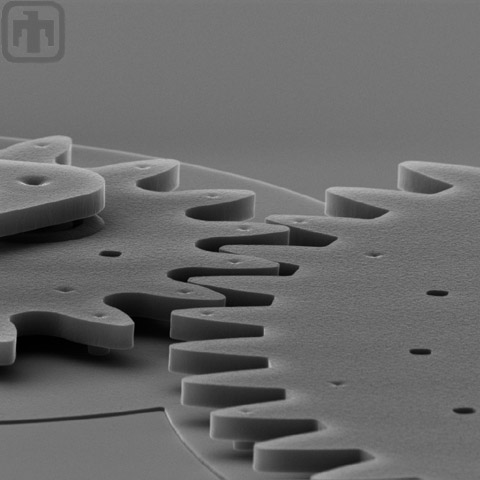
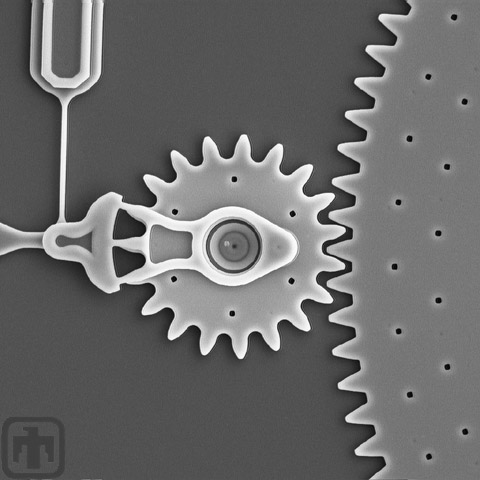
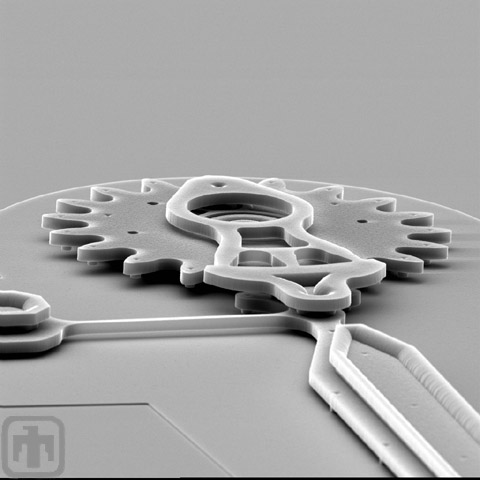
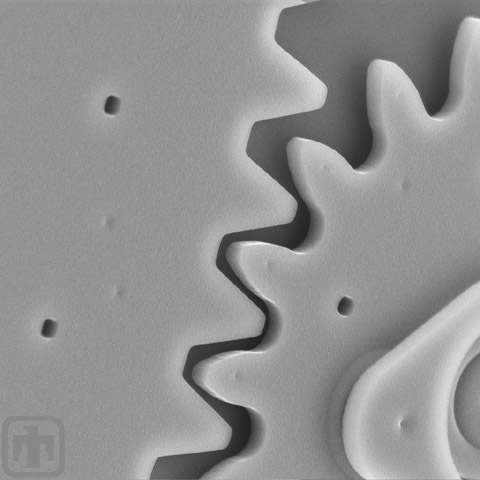
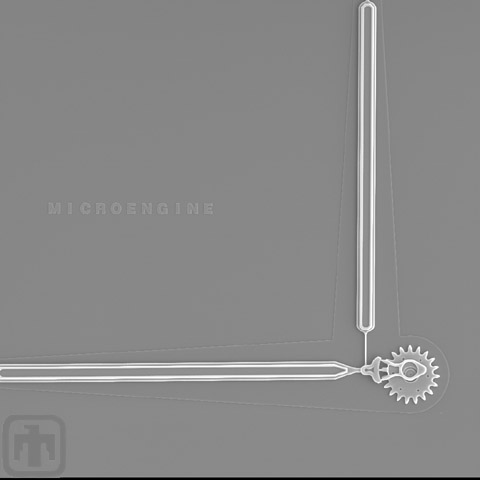
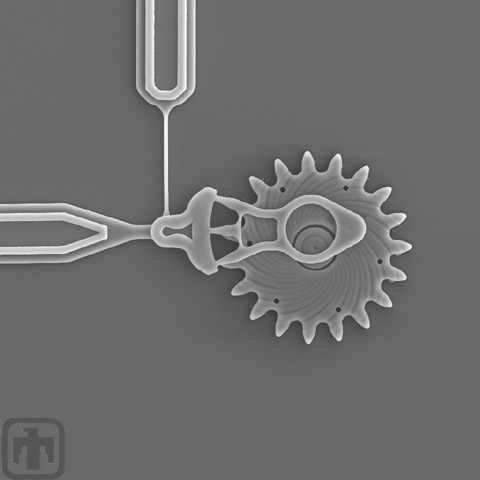
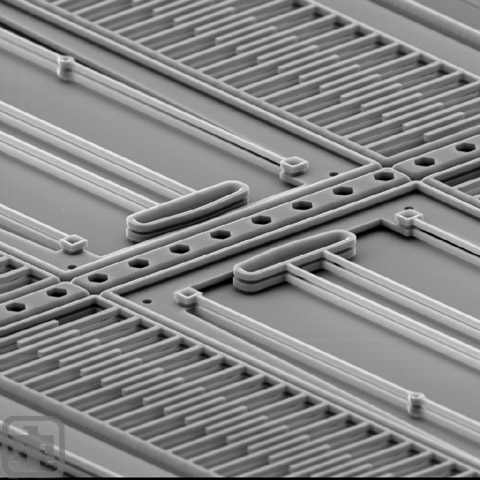
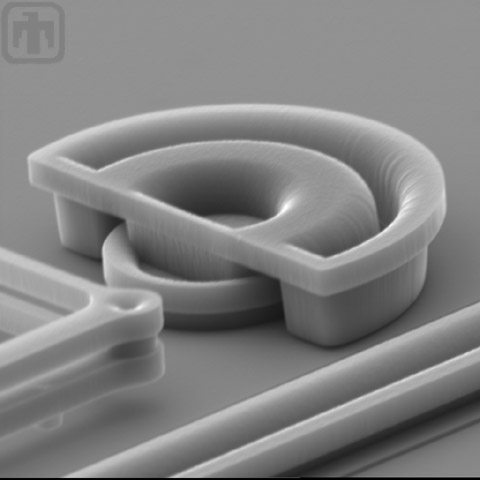
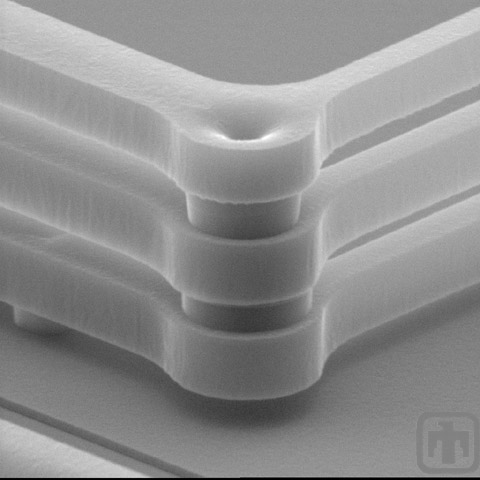
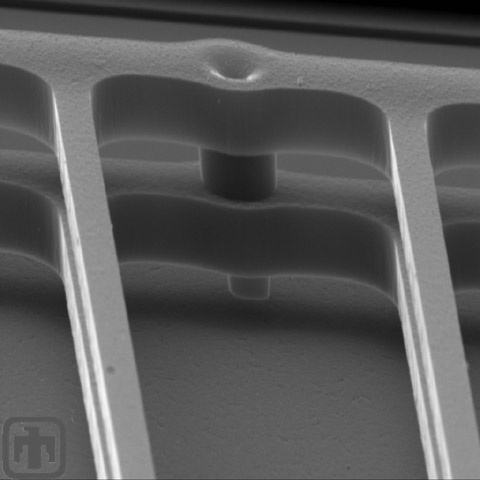
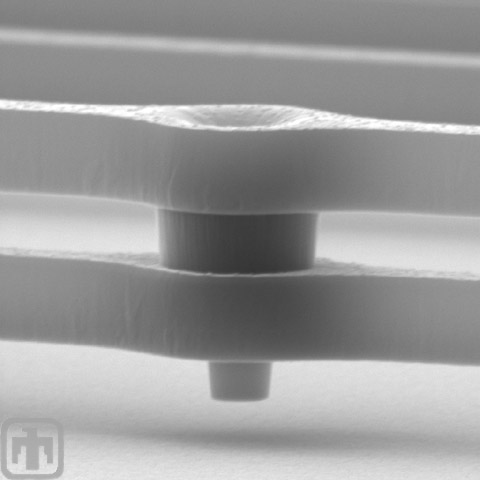
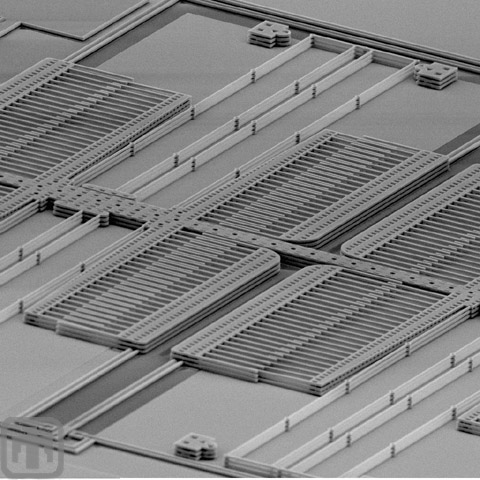
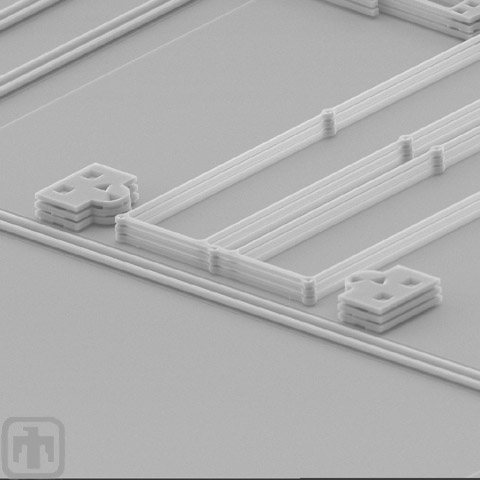
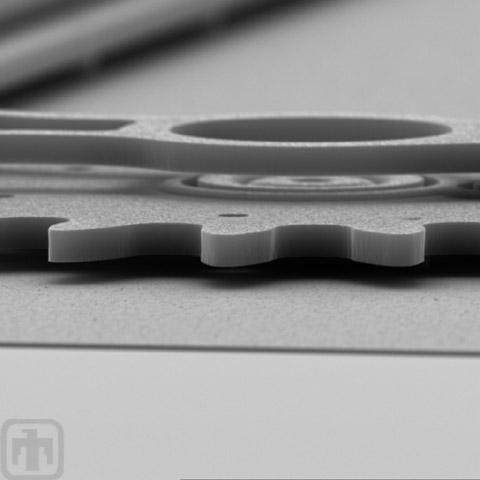
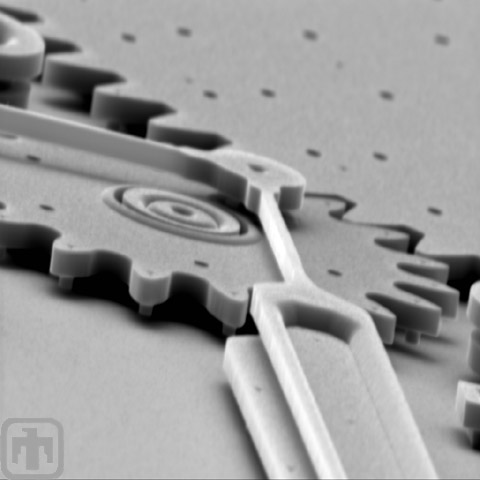
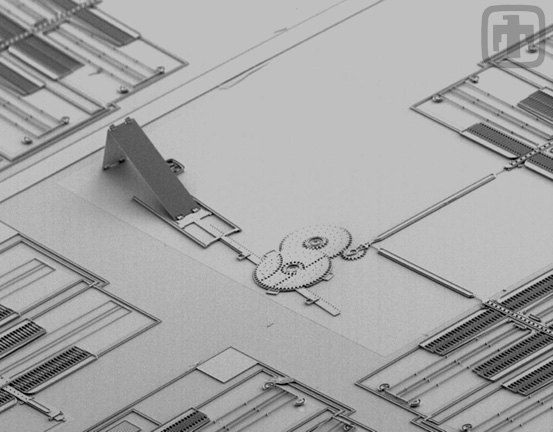
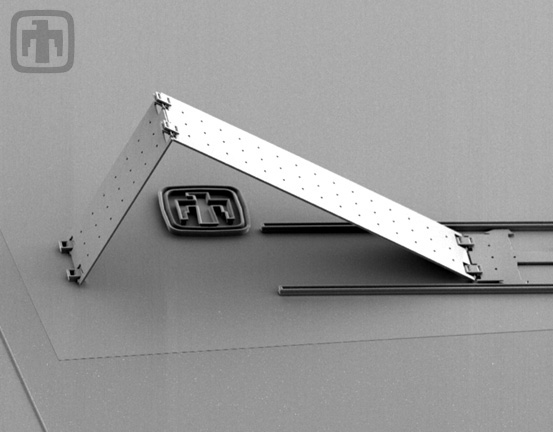
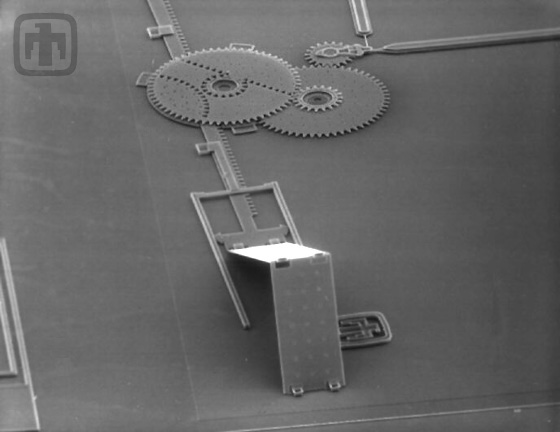
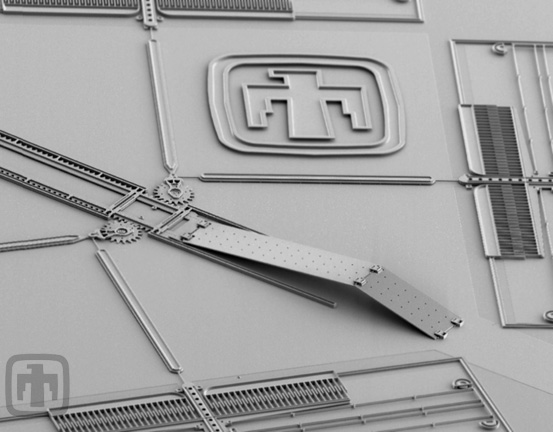
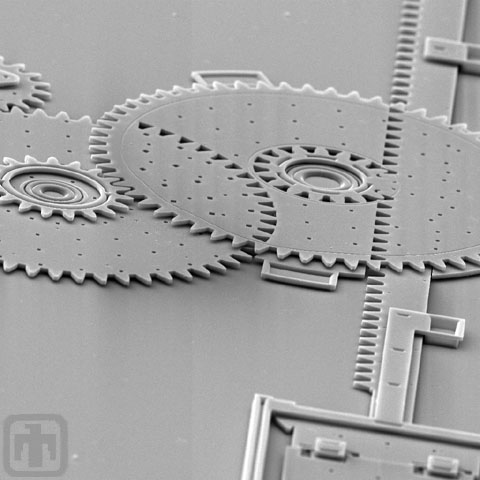
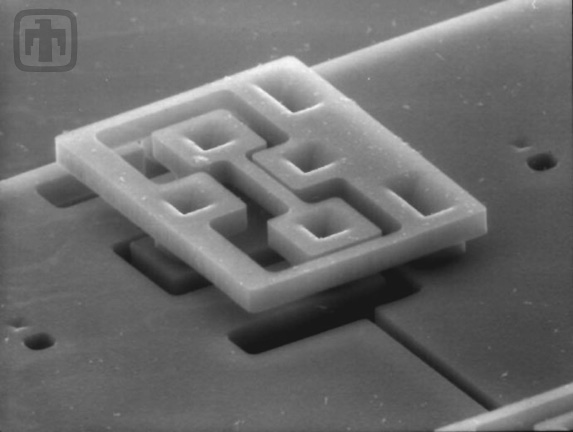
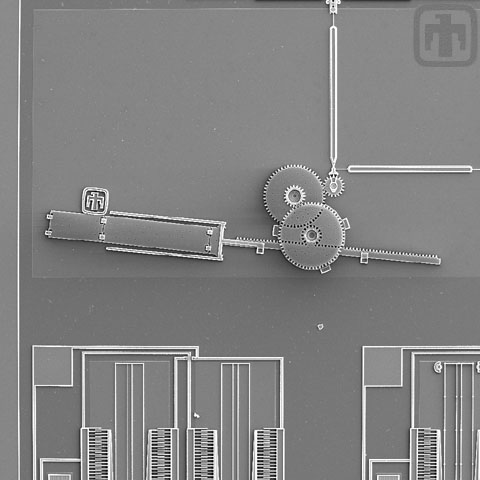
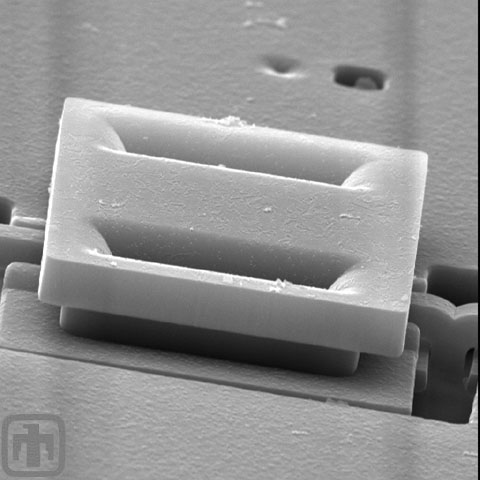
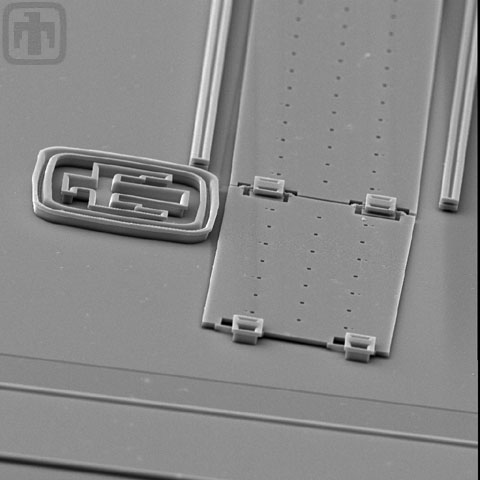
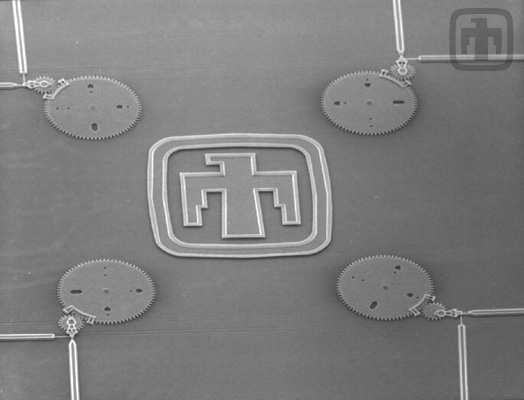
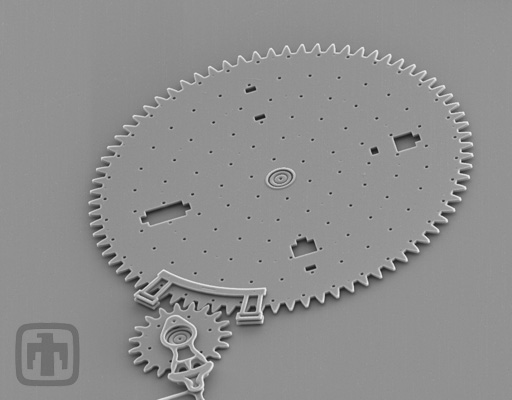
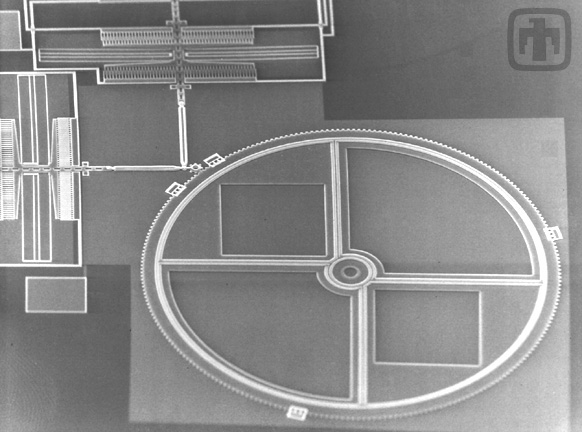
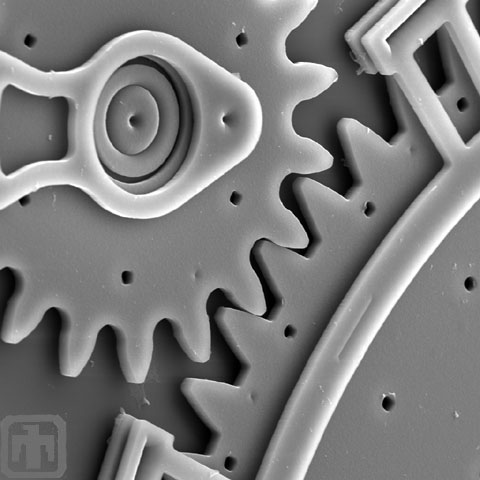
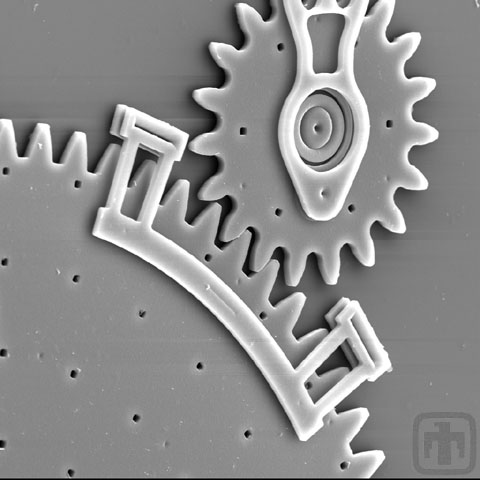
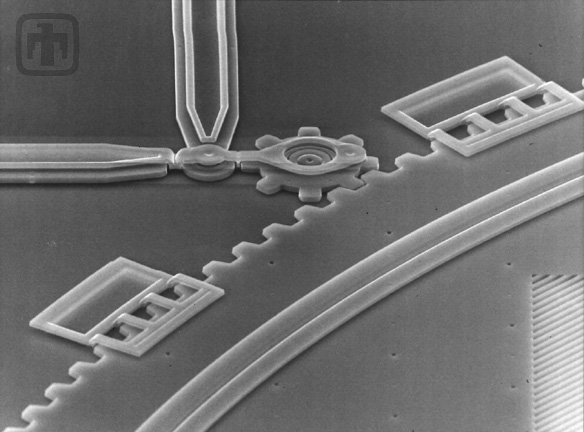
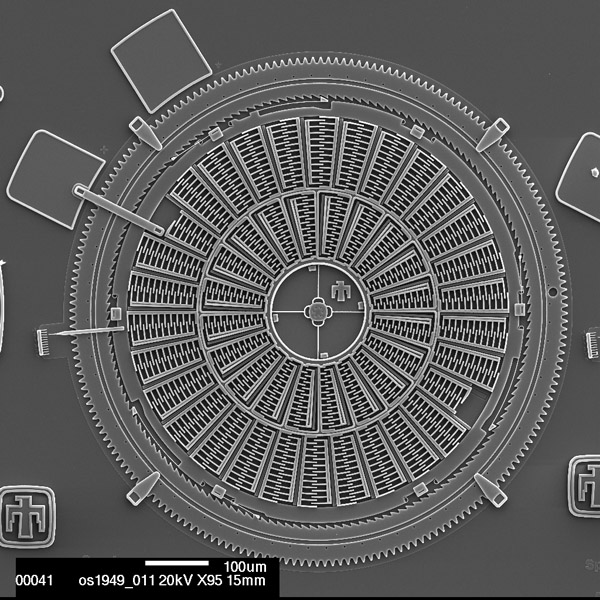
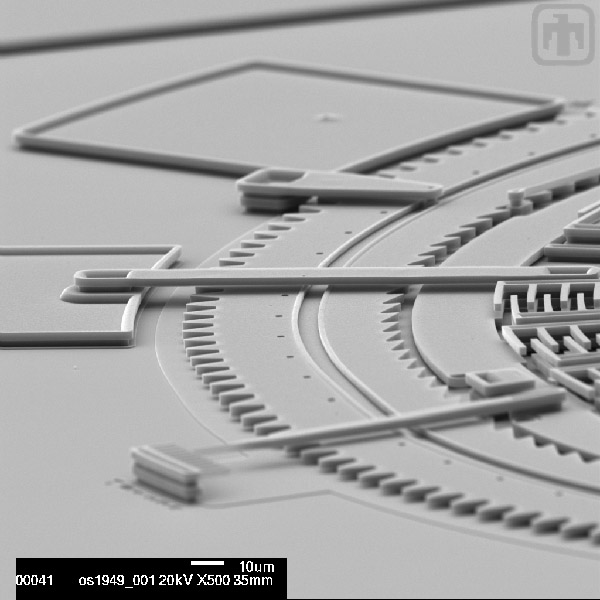
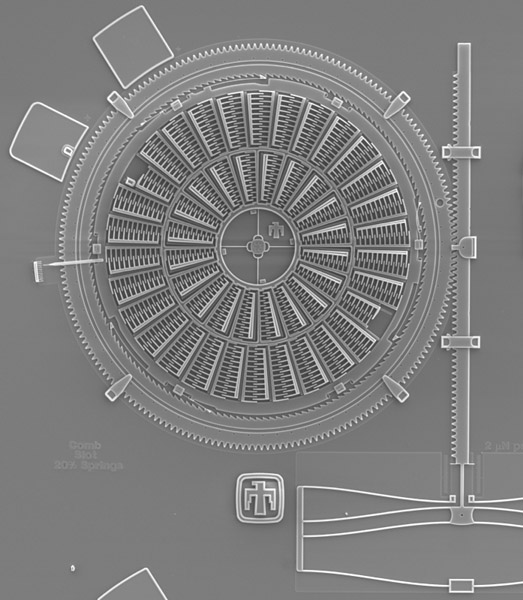
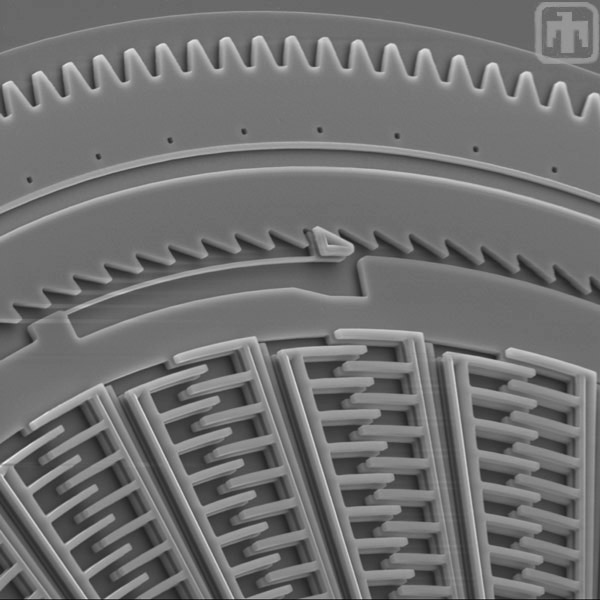
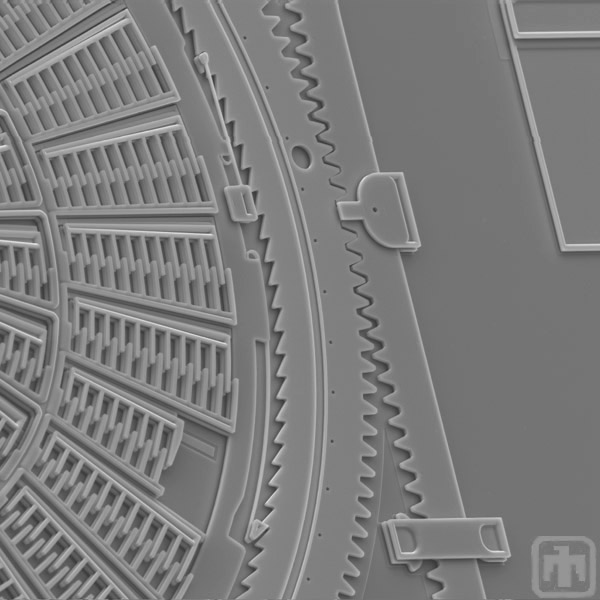
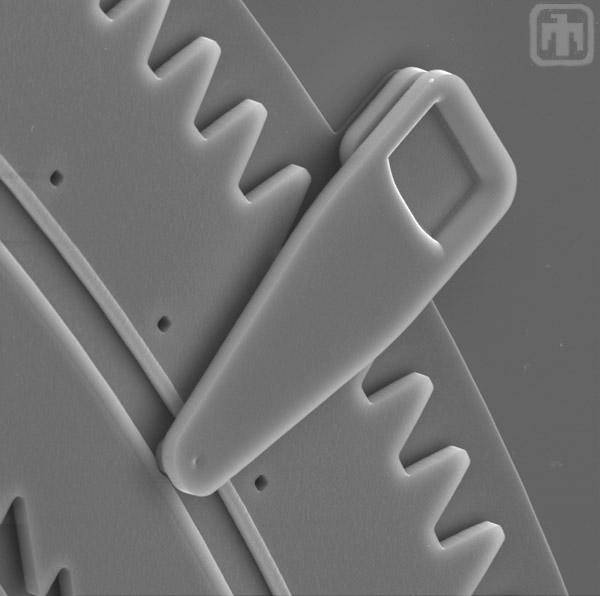
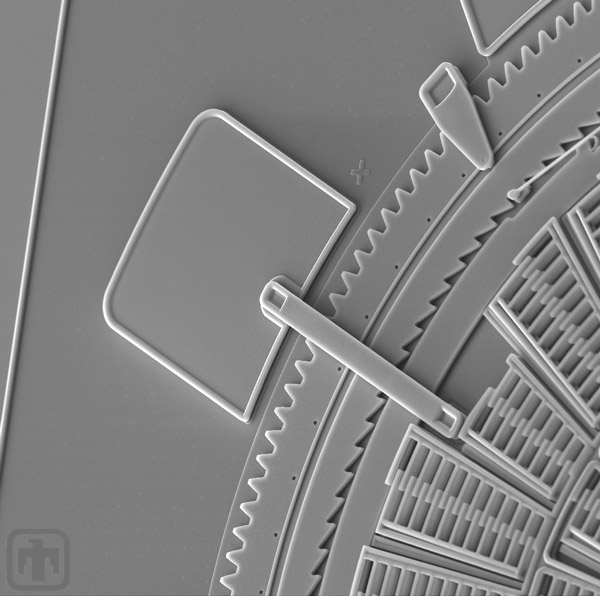
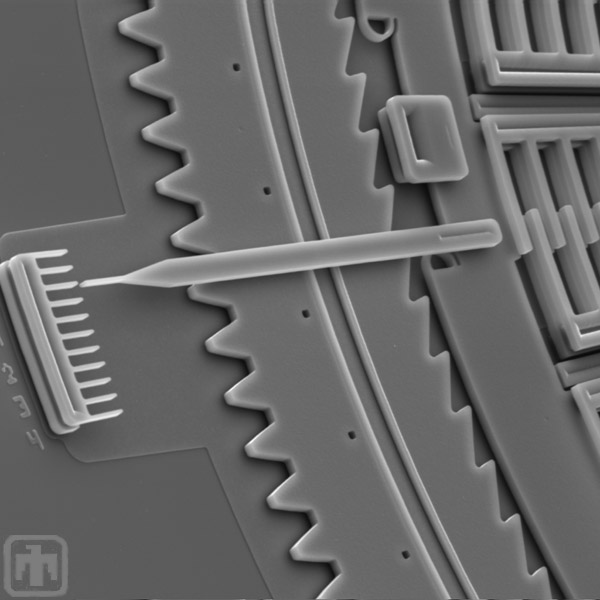
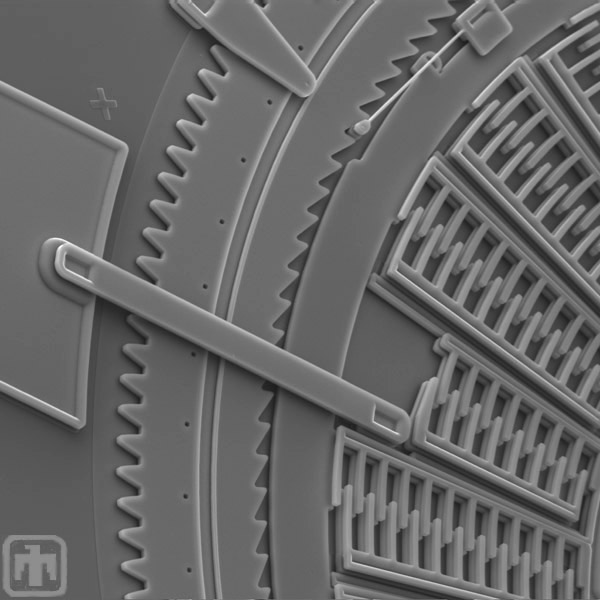
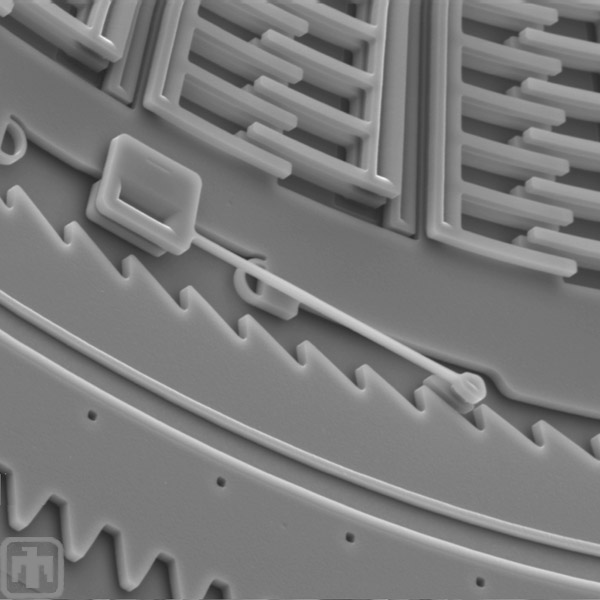